I. Introduction
UV-stabilized nonwoven geotextiles are engineered with specialized treatments to resist ultraviolet degradation3, widely applied in transportation, hydraulic, and environmental projects12. Their UV resistance and cost-effectiveness are critical factors for engineering design.
II. Performance & Lifetime Testing
‌Material Properties‌
- ‌Composition‌: Primarily polyester (PET) or polypropylene (PP)
- ‌Structure‌: 3D fibrous network offering mechanical strength (>15kN/m for 300g PET) and permeability
- ‌Durability‌: ≥90% UV stability with >20-year buried lifespan
‌Testing Methods‌
- ‌Accelerated Aging‌: Simulates UV/temperature/humidity stress via UV chambers
- ‌Field Exposure‌: Real-world monitoring (time-intensive but accurate)
- ‌Metrics‌: Track tensile strength, CBR puncture resistance (≥2.5kN for 600g PET), and permeability decay
‌Service Life‌
- ‌Buried‌: >20 years (minimal UV exposure)
- ‌Exposed‌: Reduced lifespan; protective coatings/coverings recommended
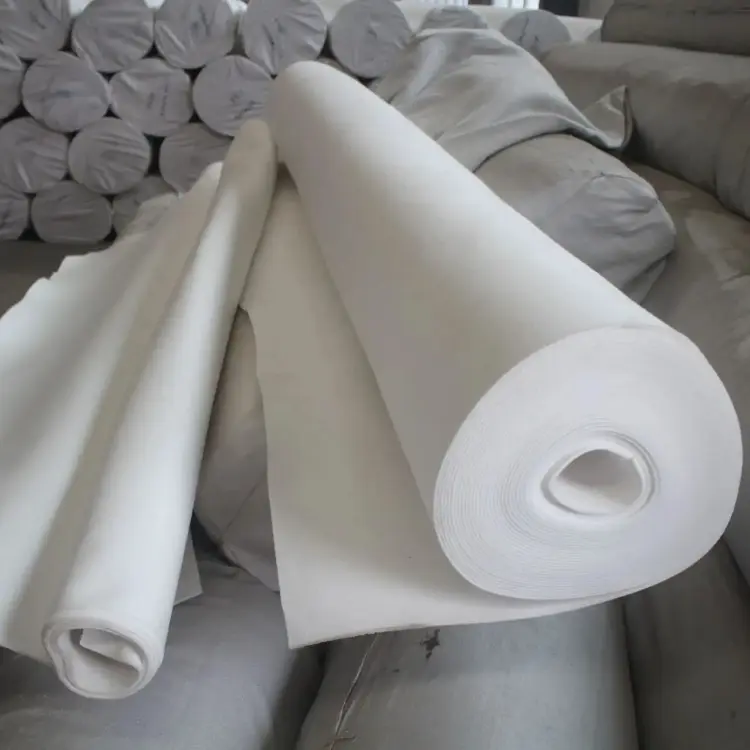
III. Cost Analysis
‌Material Costs‌
- ‌PET‌: Higher initial price (¥0.60–0.90/m² for 200g) but superior longevity
- ‌PP‌: Budget-friendly but limited UV resistance
‌Project Costs‌
- ‌Installation‌: Simple laying process (cost scales with project size)
- ‌Maintenance‌: Near-zero for buried applications
‌ROI Comparison‌
- ‌Short-term‌: PP reduces upfront costs by 20–30%
- ‌Long-term‌: PET achieves 40% lower lifecycle costs
IV. Case Studies
‌Rizhao PET Project‌
- Specifications: 150–800g/m², bulk discounts (8–12%)
- Performance: >20-year buried lifespan, 90% UV stability
‌Contaminated Site Remediation‌
- Solution: HDPE composite membranes for extended exposure
- Savings: 35% maintenance cost reduction over 15 years
V. Conclusion
UV-stabilized geotextiles balance durability and economics:
- ‌PP‌: Ideal for short-term/low-budget projects
- ‌PET‌: Optimal for critical/long-duration infrastructure