I. Pre-Construction Preparation
1. Material Preparation
- Select woven geotextile fabric based on:
- Tensile Strength (MD/CMD ≥ 20-100 kN/m per project specs)
- UV Resistance (≥70% retained strength after 500 hrs ASTM D4355)
- Permittivity (≥0.5 s⁻¹ for filtration compatibility)
- Verify compliance with ASTM D4595 (tensile) and GRI-GT7 standards.
2. Site Preparation
- Clear debris, rocks >50mm, and vegetation.
- Compact subgrade to ≥90% Proctor density; achieve surface tolerance of ±25mm/3m.
- Eliminate sharp protrusions to prevent puncture damage.
3. Equipment Readiness
- Critical machinery:
- Geotextile deployment roller system
- Mechanical seamer (for overlap joining)
- Anchoring spikes/U-pins (stainless steel, min. length 300mm)
II. Step-by-Step Construction Procedure
1. Base Layer Installation
- Place a granular cushion layer (crushed stone, 50-100mm thick) over subgrade.
- Key requirement: Particle size ≤40mm to prevent woven fabric abrasion.
2. Geotextile Deployment
- Unroll woven geotextile parallel to the primary stress direction (e.g., slope contour, embankment axis).
- Maintain ≥300mm overlap at edges; prevent folds or creases.
3. Anchoring & Tensioning
- Secure fabric every 1.5m using:
- U-pins (staggered pattern, penetration depth ≥200mm)
- Sandbags (25kg/m² at edges during windy conditions)
- Apply slight tension (<3% elongation) to avoid slack.
4. Seaming & Overlap Joints
- Method 1: Mechanical Sewing
- Use UV-resistant polyester thread (ASTM D4356)
- Stitch type: Double-lock, ≥4 stitches per 25mm
- Method 2: Heat Welding
- Temperature: 300-350°C (for PP/PE woven geotextiles)
- Pressure: 0.2-0.4 MPa
- Min. seam strength: 80% of parent material strength.
5. Protective Cover Installation
- Immediately cover with:
- Fill material: Angular aggregate (25-75mm gradation)
- Lift thickness: ≤300mm (compacted)
- Initial placement via backhoe from edge inward to prevent displacement.
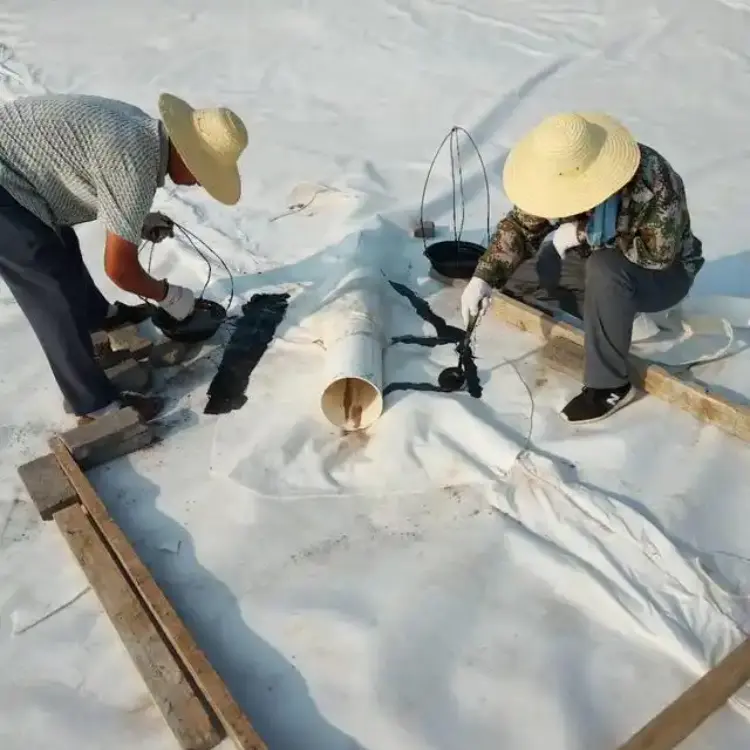
III. Critical Considerations for Woven Geotextiles
⚠️ Directionality: Align machine direction (MD) with maximum stress vector (e.g., perpendicular to slope).
⚠️ Abrasion Control:
- Prohibit tracked equipment directly on exposed geotextile.
- Use plywood mats for machinery transitions.
⚠️ UV Degradation: Limit solar exposure to ≤48 hours (cover or coat with bitumen if delayed).
⚠️ Seam Integrity: Field-test seams via vacuum chamber (ASTM D5820) or peel tests (ASTM D4884).
IV. Post-Construction QA & Maintenance
1. Inspection Protocol
Checkpoint | Acceptance Criteria |
---|---|
Seam continuity | Zero gaps >3mm |
Surface deformation | Wrinkles ≤50mm height |
Anchor spacing | ≤1.5m intervals |
Cover thickness | ≥ design thickness +10% |
2. Long-Term Maintenance
- Bi-annual audits: Inspect for:
- Clogging (clean per EN 965 flow criteria)
- Mechanical damage (patch with same-grade fabric +150mm overlap)
- Documentation: Maintain logs of strain gauges (if installed) and settlement markers.