Fiberglass geogrids, as high-performance geosynthetic materials, significantly lower project costs while enhancing structural integrity and longevity. Here’s how they achieve up to ‌30% budget reduction‌:
‌1. Extends Road Lifespan & Slashes Maintenance Costs‌
By effectively delaying crack initiation and propagation, fiberglass geogrids reduce fatigue-induced damage and ‌extend pavement lifespan by nearly 30%‌. This minimizes large-scale reconstruction frequency and lowers repair costs from reflective cracking.
‌2. Cuts Material Consumption by 30%+‌
Enhanced structural strength distributes vehicle loads evenly, reducing surface impact. This allows ‌thinner asphalt layers‌ (e.g., from 175mm to 100mm), lowering material costs by over ‌30%‌.
‌3. Accelerates Construction Efficiency‌
Lightweight design and simplified installation enable rapid deployment. In asphalt road rehabilitation, geogrids ‌shorten project timelines by 50%‌ and reduce traffic disruption.
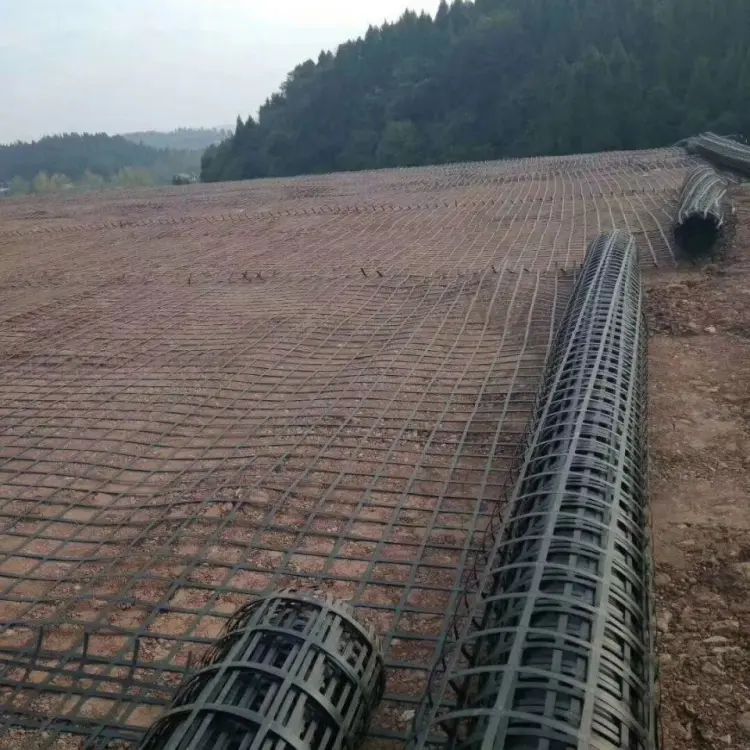
‌4. Conserves Land & Aggregate Resources‌
When reinforcing bridge abutments or railway slopes, geogrids enhance load-bearing capacity and stabilize culverts. This ‌eliminates land excavation‌ and reduces aggregate consumption by ‌>40%‌.
‌5. Reduces Long-Term Operational Costs‌
Superior weather resistance (-100°C to 1000°C) and anti-corrosion properties ensure durability. Over their lifecycle, geogrids ‌lower maintenance frequency by 50%‌ and cut total costs by ‌40%‌.
‌Conclusion‌
Fiberglass geogrids deliver transformative budget savings through:
- ‌30% lifespan extension‌
- ‌30%+ material reduction‌
- ‌50% faster construction‌
- ‌40% resource conservation‌
- ‌40% lifecycle cost savings‌
Their integration offers a sustainable, high-efficiency solution for modern infrastructure—maximizing value while minimizing ecological impact.